摘要: 文章从艇身smc热压模具设计基础、艇身smc成型工艺关键技术等方面对于某高速摩托艇艇身smc压缩模具设计与制造进行了详细的介绍。
1 艇身smc压缩模具设计与制造
1.1 艇身压缩模具设计基础
smc热固性玻璃钢压缩模是将片状玻璃纤维板料料放入成型温度下的模具加料腔,使其受热受压,成为熔融状态充满整个型腔,当塑件固化成形后,上下模打开利用顶出装置顶出塑件,从而得到所需制品,主要用于热固性塑料成型。其特点是简单、无浇注系统、料耗少、制品变形小、收缩小、各向异性小。压缩模的典型结构为固定式压缩模,其上下模都固定在压机上,开模、合模、脱模等工序均在压机内进行,生产效率高,操作简单,劳动强度小,开模振动小,模具寿命长。但其结构复杂,成本高,且安放嵌件不方便。适用于成形批量较大或形状较大的塑件。热固性塑料压缩成型需花较高的温度下进行,因此模具必须加热,常见的加热方式有电加热、蒸汽加热、煤气或天然气加热等,电加热应用普遍,但是其维修保养麻烦,且温度均匀性难以控制。高精度的smc压缩模应用较多的是采用油加热,其加热温度可保证一致性好,且成本低同时可延长模具的使用寿命。 copyright 123456
压缩模的典型结构可按如图1所示的方式分类,按与压机连接的方式可分为移动式和固定式,按照模具凸凹模配合的结构形式可分为溢式、半溢式和不溢式三种。其中不溢式压缩模又称封闭式压缩模,这种模具有加料室,其断面形状与型腔完全相同,加料室是型腔上部的延续。没有挤压边,但凸模与凹模有高度不大的间隙配合,一般每边间隙值约0.075 mm左右,压制时多余的塑料沿着配合间隙溢出,使塑件形成垂直方向的毛边。模具闭合后,凸模与凹模即形成完全密闭的型腔,压制时压机的压力几乎能完全传给塑料。不溢式压缩模的特点是塑件承受压力大,故密实性好,强度高。不溢式压缩模由于塑料的溢出量极少.因此加料量的多少直接影响着塑件的高度尺寸,每模加料都必须准确称量,所以塑件高度尺寸不易保证,故流动性好、容易按体积计量的塑料一般不采用不溢式压缩模。凸模与加料室侧壁摩擦,不可避免地会擦伤加料室侧壁,同时,加料室的截面尺寸与型腔截面相同,在顶出时带有伤痕的加料室会损伤塑件外表面。不溢式压缩模必须设置推出装置,否则塑件很难取出。如图2所示为典型的压缩模结构示意图。
123,123
不溢式压缩模一般不设计成多腔模,因为加料不均衡就会造成各型腔压力不等,而引起一些制件欠压。不溢式压缩模适用于成形形状复杂、壁薄和深形塑件,也适用于成形流动性特别小、单位比压高和比容大的塑料。例如用它成形棉布、玻璃布或长纤维填充的塑料制件效果好,不仅仅是因为这些塑料流动性差,要求单位压力高;而且若采用溢式压缩模成形,当布片或纤维填料进入挤压面时,不易被模具夹断而妨碍模具闭合.造成飞边增厚和塑件尺寸不准.去除困难。而不溢式压缩模没有挤压面,所得的飞边不但极薄,而且飞边在塑件上呈垂直分布,去除比较容易,可以用平磨等方法去除。
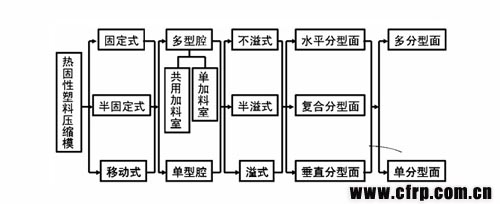
图1 压缩模典型结构分类方式
半溢式压缩模又称为半封闭式压缩模,这种模具具有加料室.但其断面尺寸大于型腔尺寸。凸模与加料室呈间隙配合.加料室与型腔的分界处有一环形挤压面.其宽度约4—5 mm。挤压边可限制凸模的下压行程,井保证塑件的水平方向毛边很薄。半溢式压缩模的特点是模具使用寿命较长。因加料室的断面尺寸比型腔大,故在顶出时塑件表面不受损伤.塑料的加料量不必严格控制,因为多余的塑料可通过配合间隙或在凸模上开设的溢料槽排出。塑件的密度和强度较高,塑件径向尺寸和高度尺寸的精度也容易保证简化加工工艺。当塑件外形复杂时,若用不溢式压塑模必造成凸模与加料室的制造困难.而采用半溢式压塑模则可将凸模与加料室周边配合而简化。半溢式压缩模由于有挤压边缘,在操作时要随时注意清除落在挤压边缘上的废料,以免此处过早地损坏和破裂。由于半溢式压缩模兼有溢式压缩模和不溢式压缩模的特点,因而被广泛用来成形流动性较好的塑料及形状比较复杂、带有小型嵌件的塑件,且各种压制场合均适用。溢式压缩模由于其成本低,常用于制件技术含量低要求不高的场合。
内容来自123456
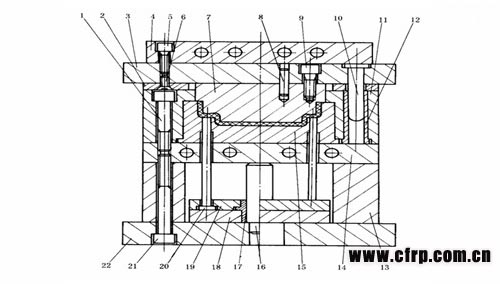
1 内六角螺钉 2 承压板 3 上模座板 4 加热板 5、9、21 内六角螺钉 6沉头螺钉 7 凸模
8 圆柱销钉 10 导柱 11 凹模固板 12 导套 13垫块 14支承板(加热板) 15 凹模 16推板导柱
17 推板导套 18 推板 19推杆固定板 20推杆 22下模座板
图2 压缩模的典型结构示意图
1.2艇身smc热压模具设计与制造
smc压缩模由型腔、导向机构、侧向分型抽芯机构、脱模机构、加热系统等机构组成。其中型腔是直接成型塑件的部位,型腔与加料室共同起装料的作用。导向机构用来保证上下模合模的对中性。保证推出机构上下运动平稳。在成型带有侧向凹凸或侧孔的塑件时,模具必须设有各种侧分型抽芯机构,塑件才能抽出。固定式压缩模在模具上必须有脱模机构 (推出机构)。smc压缩模设计的关键是其凸模与凹模配合结构形式,典型的包括溢式压缩模,其凸、凹模无配合,凸、凹模接触面应光滑平整,但不宜太大,设计成宽3~5mm环形面,但这样环形面易损。不溢式结构其凸凹模配合间隙与配合高度要适当,太小则排气困难,凸、凹模易擦伤,太大则溢料严重,飞边难去除。半溢式结构其因带有水平挤压面,挤压面宽度不应太小。为使余压全部由挤压面承受,必须设承压块。现代产品成型工艺中因溢式压缩模的固有缺陷,其应用较少。应用较多的是半溢式和不溢式两种结构。
copyright 123456
摩托艇艇身覆盖件是目前国内最大的smc模压件,加上其外形结构复杂、镶嵌件多、成型难度高、配合精度高、耐海水腐蚀等要求;同时承受着艇的各种运行工况作用,因而要求重量轻、比强度高。采用传统的手糊成型工艺不仅产品质量差、技术含量低、一致性差,而且存在劳动强度高、生产效率低、制造成本高等缺陷。艇身采用smc片状模塑料压制成型,将填补国内采用此种方法成型全smc复合材料艇身的空白。采用钢板拼焊整体模具设计制造,通过油循环加热实现smc艇身的热模压,实现smc艇身的大批量无余量生产。smc模压最核心的主要依赖于模具的结构设计、模压的时间、压力温度等工艺参数的合理制定、热变形的校正措施等。
ugnx提供了基于专家系统的注塑模(mold wizard)、钣金零件冲压模(die engineer)、级进模(progressive die wizard)等模具设计功能,模具专家设计系统融入了模具设计师的经验和系统开发师的智慧,使用它们可以加速模具设计速度,提高产品的设计质量。模具设计向导技术提供了基于最优实践基础上的、逐步引导式进行构造的工作流程,使许多企业的模具设计过程实现了自动化。使得企业在模具设计制造(规划、采购、详细设计、电极设模具制造)的并行展开,因而缩短了交付时间。由于艇身smc热成型压缩模在模具的结构设计上与注塑模有相似的地方,因此在进行艇身热压模具设计时,充分利用注塑模(mold wizard)模具设计的相似性解决模具分模,模具结构设计方面的设计工作。
123456
如图3所示为对该艇身smc模压成型的模具设计、模具数控加工编程以及模具实物。该模具结构为封闭式、油循环加热成型艇身。此种结构较开放式、电加热型模具,其产品重量可以严格控制、无飞边、壁厚一致性好、加热均匀、维修维护方便、模压能耗低等多种优点。模具设计最主要的为凸凹模凸凹模之间的接口配合设计对溢料飞边的影响、加热系统的设计、顶出机构与模具的表面光洁度与修配余量的控制。
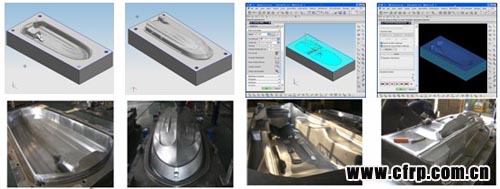
图3 摩托艇艇身模具设计制造与实物
2 艇身smc模压成型工艺关键
压缩模塑前的准备的工作包括模具调整、预压。压缩模塑过程中对于大的嵌件应预热;关键是加料量应准确。凸模为接触塑料前应快,接触后要慢。排气应安排在塑料未固化前,速度要快。固化速度和固化程度要适当,使制品性能好,生产效率高。要控制两个参数是固化速度和固化程度。固化速度过快容易导致充模不满;过慢则生产周期长,生产效率低。固化程度不足则导致力学强度、耐蠕变性、耐热性、化学性能下降;固化过度则导致力学强度不高,脆性大,变色,表面有气泡。脱模剂的选用在每件制品模压前也起着重要的作用,同时在模具清理时可用铜刀或铜刷去除残留物,用压缩空气吹净模具。
本文来自123
压缩模塑成型的压力在整个成型过程中,压力的变化与压缩模类型有关。成型压力主要根据塑料种类、塑料形态、制品形状及尺寸、成型温度和压缩模结构等确定。提高压力,利于充模,但太高,易损坏嵌件与模具。成型时模具温度,比热塑性塑料模温更重要。型腔内热固性塑料最高温度大于模具温度;热塑性塑料低于模温。模压时间与成型温度有关,成型温度越高,时间越短。还与塑料种类、制品形状及厚度、压缩模结构、预压和预热、成型压力等有关。模压时间太长,会产生过熟,导致制品强度下降,过短,则欠熟。
艇身smc模压过程中的关键要素分别为填料、加压、温度、保温时间、起模、模具润滑等。其中smc原材料对模压的有着重要的影响,如s35/1039/1046三种不同的材料,其模压的过程控制不同。如s35的材料,其综合机械性能高,纤维含量高且纤维丝较长,树脂含量低,其热模压时成型流动比较困难,因此在铺料时要求铺料要尽可能的均匀分布。1039则综合机械性能较低,树脂含量高,成型流动性好,但是脆性大。而1046这种类型的材料,综合机械性能适中,树脂含量和纤维含量适中,该材料的综合机械性能与成型工艺性能介入s35与1039之间,是比较适合大型薄壁壳体的成型的。从上述分析来看,在选择模压工艺前,首先要对纤维、树脂的含量对成型工艺性、机械性能等方面分析,从而能够比较好的确定其模压工艺参数与过程控制。
123,123
艇身smc模压常见的缺陷主要包括重量超标或者过小、表面出现裂纹、表面光洁度不够、表面颜色不均匀且有些部位出现黄色、脱模不顺畅有时出现粘模的现象。针对上述情况在试模时的填料在理论计算的基础上通过工艺试验验证的方法进行合理的控制,同时配制样板在smc板料的基础上对填料进行控制下料称重。模具表面温度通过温度测量计对多处关键点的温度进行测量,根据温度分布均匀的需要,对模具加温和流道等进行合理的设计制造来保证,在设计初期可通过有限元模拟的方法对流道进行传热分析模拟优化设计,有效的保证了模压时模具温度的均匀一致性。针对模压后,由于产品取出后为高温达120o左右状态,因此对脱模后的产品为保证产品的外形和减小冷却过程中的变形,通过校形铺放工装有效的保证了产品的外观尺寸精度一致性要求。如下图所示为艇身模压出的实物图,经过装配粘接与水上试验,通过smc成型的方式,不仅有效的减轻了整艇的重量,同时有效的保证了产品的密封性、行驶的稳定性和使用强度与疲劳要求,如图4所示为压制成型合格后的实物。
内容来自123456
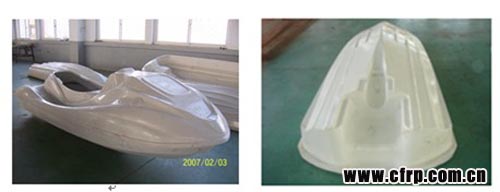
图4 艇身模压实物图
3 结束语
本文重点对某高速摩托艇为例,对其艇身smc压缩模具设计与制造进行了重点介绍。希望能为读者提供一些借鉴。
参考文献
[1] 中国模具设计大典(第五卷),黄乃瑜等,2003,江西科学技术出版社.
[2] 模具设计基础及模具,李建军等,2006,cad机械工业出版社.
[3] 材料成型工艺,夏巨葚等,2005,机械工业出版社.
中国航天科工集团第九研究院红阳机械厂(湖北孝感 432100)