国家排放法规越来越严格,各地实施计重收费治超政策,卡车轻量化成为解决“超载”、促进“节能减排”的契机。大功率、轻量化、低油耗、经济性重卡成为市场需求的主流。
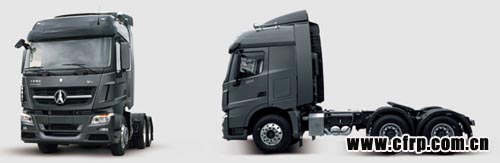
北奔在今年北京车展上展示的V3轻量化牵引车(H09)自重低于8吨。通过优化并匹配动力传动、制动、转向、车电及发动机辅助系统等不同成本的系列化模块,组合形成4x2、6x2、6x4、8x4四种驱动型式的牵引车、载货车、自卸车系列车型。
近日,由包头德翼、北京蓝星、中材科技共同研制的高科技复合材料首次在国内卡车车厢中成功应用,实现了我国轻量化卡车车厢从无到有的跨越,使我国复合材料在汽车轻量化领域的应用技术达到国际领先水平。
copyright 123456
该复合材料车厢较对应的金属车厢减重40%,其碳纤维拉挤型材制造成本低,质量稳定,纤维含量高、强度大,针对不同的使用条件可以进行灵活的结构和铺层设计,是一种极具市场竞争力的产品,可作为未来先进结构材料的基础产品,有着广阔的发展空间。
近年来,随着我国高速公路网络的增长,重型卡车在运输效益方面的优势突显,刺激重型卡车市场高速增长。2011年,我国重型卡车产销量超过100万辆,全国保有量达到约近500万辆。公路货运车辆在向大吨位、多轴方向发展的同时,超载、高能耗、高污染等问题也日益突出,而随着全国公路交通节能环保要求的提出及货运车辆计重收费政策的全面实施,重型卡车轻量化技术研究被迅速提上日程。重型卡车轻量化在保证卡车强度和安全性能的前提下不仅可以降低卡车整备质量、增加装载质量,提高卡车运营能力、降低能耗、减少二氧化碳及其他污染物排放,同时也可减少货运行业中的超载现象,确保行车及道路安全,具有经济、环保和安全三重效益。
123456
2010年年初,卡车轻量化项目团队承担了卡车轻量化车厢的研发、设计工作,力图攻克复合材料抗冲击性差、耐磨性差、刚度低等技术难点。该项目团队以现有金属材料车厢为起点,通过数据建模、有限元分析,进行复合材料车厢的结构设计及分析验证,延伸结构材料研发和纤维含量高、强度大、有广阔发展空间的拉挤型材的研发,在原有拉挤设备基础上进行配套改造,经多次工艺调试,成功生产出连续的大丝束碳纤维拉挤型材。该项目还引入新材料聚双环戊二烯(PDCPD),提高了复合材料表面附着层的性能。研发成功的复合材料通过在国内8.6米自卸车概念车车厢中的应用和分析,各项数据均超过国内指标。据介绍,该项目符合国家产业发展政策,采用复合材料汽车车厢,减轻了汽车自重,节约了能源,发展前景广阔、社会效益明显。